L et us begin at the beginning. The clay arrives as a slip (a suspension of clay in water) from Hodges Minerals Ltd. in St. Elizabeth. It has been dried, crushed and ball milled under careful supervision at the plant. This particular clay is called Frenchman Clay and is dug from the west banks of the Black River some ten to twenty feet below the surface at a village named Slipe on the Frenchman peninsular and taken to Hodges for processing. We mix this clay, which is essentially a mixture of white refractory (high temperature) clay and quartz sand, in exact proportions with a sand containing a
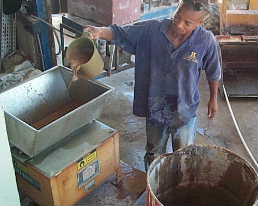
high proportion of feldspar (granodiorite) from Temple Hall in St. Andrew or in recent times imported feldspar. Prior to blending with the clay the Temple Hall sand is washed and magnetic iron (magnetite) extracted - picture at left shows the magnet - and milled separately for use as a glaze and decorative slip pigment and for onglaze painting. The iron can be seen as those reddish brown brush marks and splashes mainly on the sides and rims of our work. Now back to the clay preparation. The slip is examined for density (ratio of solids to water), pH and fluidity after which, if the properties are acceptable, the slip is sieved and made ready for casting. If however,
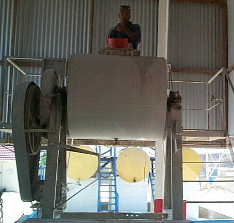
the slip is only slightly off (and this is so sometimes) it can cause unbeliveable problems as the process is technically very demanding. Casting is employed in our studio as it is the only method available to us that is able to produce small affordable pieces in reasonable numbers and at reasonable cost. Casting produces a considerable amount of scrap from trimmings and damaged pieces and this is sorted and recycled as casting slip, engobes (decorative slip) and throwing clay. Very little is wasted. The Hodges ball mill is shown at right.